Aluminum is
the metal of choice for weight savings in the cylinder block, but the performance requirements and
manufacturability issues will drive the choice of a specific aluminum alloy.
-
There are a range of different alloys that are commonly used for
aluminum castings.
-
The
engine designer has to select the aluminum alloy that offers the best combination of mechanical properties,
castability, and machinability.
|
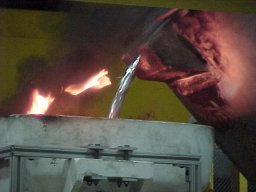 |
Aluminum being
poured into the mold |
|