Foam Pattern Decomposition |
As the metal is poured into the
mold, the heat of the advancing melt front progressively collapses,
melts, depolymerizes, and vaporizes the polystyrene foam.
|
Collapse --
100C / 212
F
>>>
Melt -- 165C / 330 F >>>
Depolymerize -- 315C / 600F >>>
Vaporize -- 576C / 1069F |
|
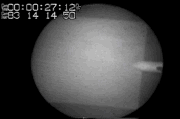 |
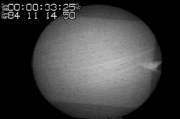 |
Movie of Metal Flow into Low Fusion Foam |
Movie of Metal Flow into Full Fusion Foam |
|
The density and fusion
condition of the foam affect how the foam decomposes.
--- If
the foam is underfused, it will decompose non-uniformly and metal
flow into the mold will be fast and turbulent, trapping residue
and causing fold defects and pores.
--- Fully
fused foam will decompose evenly and produce smooth, uniform metal
flow with no defects or trapped residuals. |
Flaw-free
castings require controlled metal flow and consistent foam density
and bead fusion. |
|
|