Table of Contents
Recognizing the impact of physical alloy characteristics and mechanical characteristics at the outset will help the design engineer avoid many of the pitfalls in making the assumption that any one alloy can be treated like any other alloy.
Metallurgical Characteristics
Fluid Life
A molten metal’s fluid life is more than its ability to fill the mold cavity. The fluid life also determines how easily and how long the metal flows through narrow channels to form thin sections, and how readily it conforms to fine surface detail.
The temperature of the molten metal is not the only factor that affects the alloy’s fluid life. For a give alloy, fluid life does not increase with superheat (excess temperature above the alloy’s liquidus temperature). However, fluid life of every alloy does not necessarily increase equally with temperature. In other words, fluid life of a molten metal alloy is also dependent on chemical, metallurgical and surface tension factors.
Fluid life will affect the design characteristics of a casting. By understanding the nature of an alloy’s fluid life, the designer will recognize several important design criteria. Some of these are:
- minimum section thickness that can be attained
- the maximum length of a thin section
- the fineness of cosmetic detail that is possible
It is also essential to understand that moderate or even poor fluid life does not limit the cost-effectiveness of design. Knowing that an alloy has limited fluid life tells the designer that the casting should feature:
- softer shapes
- finer detail in the bottom portion of the mold
- more taper leading to thin sections
- larger lettering
- etc.
Some casting processes feature molds that are very dry or hot. These molding process minimize the effects of convection, a mode of heat of heat transfer which reduces fluid life.
Solidification Shrinkage
There are three distinct stages of shrinkage as molten metal alloys solidify:
- liquid shrinkage
- liquid-to-solid shrinkage
- solid shrinkage
Liquid Shrinkage is the contraction of the liquid before solidification begins. While important to metalcasters, it is not an important design consideration.
Liquid-to-Solid Shrinkage is the shrinkage of the metal as it goes from the liquid’s disconnected atoms and molecules to the formation of crystals of atoms and chemical compounds, the building blocks of solid metal. The amount of solidification shrinkage varies a great deal from alloy to alloy. Figure 1 provides a guide to the liquid-to-solid shrinkage of the most common ferrous and nonferrous alloys. As shown, shrinkage can vary from very little to high shrinkage volumes. Alloys can be further classified into three groups based on their solidification range:
- directional
- eutectic
- equiaxed
Failure to recognize the impact of liquid-to-solid (solidification) shrinkage is one of the worst errors that “rule of thumb” design handbooks make.
Liquid-to-Solid shrinkage is an extremely important consideration for the design engineer. In some alloys, disregard for this type of shrinkage results in voids in the casting. Both the design and foundry engineer have the tools to combat this problem, but the designer has the most cost-effective tool, that is geometry.
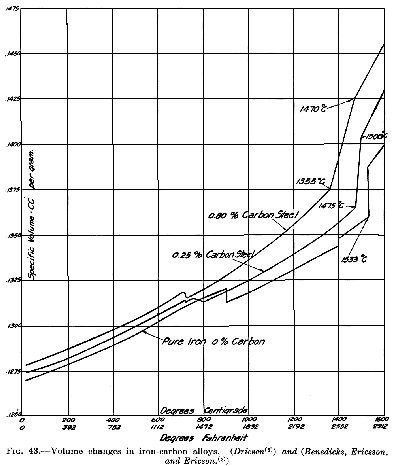
Geometry can be found that meets structural needs and solidification shrinkage needs. For some alloys, finding that geometry can be very simple. For other alloys, finding that geometry is the real essence of good casting design. Should that geometry not be found for difficult alloys, the foundry engineer must resort to “thermal trickery” to create fluid flow and heat transfer patterns that the geometry fails to provide.
“Thermal trickery” is creative stuff, a major weapon in the expert foundry engineer’s arsenal, but it is expensive. Eliminating thermal trickery with good design makes castings that cost less to produce and cost less to process and assemble.
Solid Shrinkage (often called patternmaker’s shrink) occurs after the metal has completely solidified and is cooling to ambient temperature. Solid shrinkage changes the dimension of the casting from those in the mold to those dictated by the rate of solid shrinkage for the alloy.
In other words, as the solid casting shrinks away from the mold walls, it assumes final dimensions that must be predicted by the patternmaker. This variability of patternmaker’s shrink is a very important design consideration.
This uncertainty about patternmaker’s shrink is why foundrymen normally recommend producing a first article (sometimes called a sample casting) to establish what dimensions really are before going into production. There is high risk in assuming that the solid shrinkage predictions built into patterns/dies and coreboxes will result in final dimensions that are “close enough” to prediction to fit within allowable tolerance.
Despite all the good planning, the nature of patternmaker’s shrink is unpredictable enough and important enough that adjustments will probably be necessary on the pattern to achieve the final production dimensions and tolerances.
Slag / Dross Formation
According to the dictionary, slag and dross are synonyms meaning: “refuse from melting of metals “. Obviously, no one wants “refuse” in castings.
Among foundrymen, slag and dross have slightly different meanings. Slag is usually is associated with the higher melting point metals (ferrous metals) and is composed of liquid nonmetallic compounds (usually fluxed refractories), products of alloying and products of oxidation in air. Dross, on the other hand, usually is associated with lower melting point metals (non-ferrous alloys) and often means the nonmetallic compounds produced primarily by the molten metal reacting with air.
Some molten metal alloys are much more sensitive to slag/dross formation than others. Castings made from these alloys are much more prone to contain nonmetallic inclusions. There are casting processes, quality control techniques and design considerations that can dramatically reduce the likelihood of nonmetallic inclusions in casting. Design geometry guidelines to minimize the possibility of nonmetallic inclusions affecting the surface quality of castings …
Pouring Temperature
Metal castings are produced in molds that must withstand the extremely high temperature of liquid metals. Interestingly, there really are not many choices of refractors to do the job. As a result, high molten metal temperatures are very important to casting geometry as well as what casting process should be used.
The following is a summary of common foundry alloys and their pouring temperatures:
Pouring Temperature Chart | ||
---|---|---|
Alloy | °F | °C |
Solder | ~450 | ~230 |
Tin | ~600 | ~300 |
Lead | ~650 | ~345 |
Zinc Alloys | 650-850 | 345- 455 |
Aluminum Alloys | 1150-1350 | 620- 735 |
Magnesium Alloys | 1150-1350 | 620- 735 |
Copper-base Alloys | 1650-2150 | 900-1180 |
Cast Irons; Gray, Ductile | 2450-2700 | 1340-1480 |
Monel (70 Ni, 30 Cu) | 2500-2800 | 1370-1540 |
Nickel-based Superalloys | 2600-2800 | 1430-1540 |
High Alloy Steels | 2700-2900 | 1480-1600 |
High Alloy Irons | 2800-3000 | 1540-1650 |
Carbon & Low Alloy Steels | 2850-3100 | 1565-1700 |
Titanium Alloys | 3100-3300 | 1700-1820 |
Zirconium Alloys | 3350-3450 | 1845-1900 |
For practical purposes, sand and ceramic materials with their refractory limits of 3,000 – 3,330°F (1650-1820°C) are the most common mold materials used today.
As the temperature of the molten metal alloy increases, design consideration must be given to heat transfer problems and thermal abuse of the mold itself.
Metal molds, such as those used in diecasting and permanent molding, also have temperature limitations. In fact, most of the alloys on the list are beyond the refractory capability of metal molds (except for special thin geometry designs, alloys from the copper-base group and up require sand or ceramic molds).
Carbon and low alloy steels approach the limit of sand and ceramic refractories and titanium and zirconium alloys go beyond it, creating special situations. So, it is easy to see the abuse that sand and ceramic molds are subjected to when pouring temperatures approach the refractory limits. The same holds true for lower temperature molten metal alloys that approach the refractory limit of plaster or metal molds.
Again, there are design considerations that will compensate for thermal abuse and hot-spot problems in the mold. These are covered in more detail later in this section.
Mechanical Characteristics
Modulus of Elasticity
The measure of stiffness of a metal itself (without regard to material shape) is known as the modulus of elasticity or Young’s Modulus. In the case of metals, it is a function of metallurgy, and it is a mechanical property of the metal alloy.
Although this is a parameter discussed at length in engineering books on material science, it is a common measurement in foundries; in most foundries, the modulus of elasticity is a parameter measured virtually every day. The modulus of elasticity is similar to the elastic (straight-line) portion of the stress/strain diagram created whenever a test bar is pulled on a tensile test machine.
more needs to be add here Figure 4 and Figure 5 must be included somehow.
Another important design engineering fact about modulus of elasticity is that it is independent of metal shape, that is, casting geometry.
Section Modulus
Another measure of stiffness is section modulus, which is stiffness from shape or geometry; unlike modulus of elasticity, it has nothing to do with the material.
Actually, section modulus is an aspect of moment of inertia which is a function of a shape’s cross-sectional area in combination with its height.
Two important conclusions can be drawn from the mathematics:
- The only factors in the equations are shape!
- The final equation gives the engineer clues about how the shape of the I-beam could be varied to maximize moment of inertia and therefore the section modulus while minimizing the amount of material in the beam.
Stiffness from geometry of section modulus is a very powerful engineering tool. The knowledge of section modulus enables the engineer to create metal shapes that are much stiffer than the material itself could ever be.
The most significant observation that can be made about stiffness from geometry is that there is no other method besides metal casting that can offer so much geometry in the design and manufacture of component shapes.
Another significant observation is that design stress in a structural part is directly related to section modulus. In fact, it is a direct, inverse relationship in which increasing section modulus decreases stress.
We now see an important synergism between modulus of elasticity and section modulus. Modulus of elasticity determines how much stress a metal can safety carry before it begins to deform permanently and section modulus enables the engineer to use geometry to keep the stress within safe bounds. As we have learned, creative use of section modulus enables relatively weaker metals to do the work of stronger ones.
The development of engineering computer hardware and software for making and analyzing solid models has enabled a quantum leap in the use of section modulus to increase the stiffness of structural components and reduce the stress within them. In fact, these tools are making the power of metalcasting geometry much more accessible to design engineers because they enhance so significantly the ability to visualize in three dimensions.