This month’s Casteel Commentary considers the exciting opportunities for steel foundries with the development of additive manufacturing. Additive Manufacturing (AM) is being oversold as a direct replacement for steel castings. Our industry correctly feels the heat from purchasers and designers who believe that they will be able to avoid most of the historic challenges of using castings with AM parts. Instead of being threatened by AM, we need to recognize how much of an advance AM will be to make castings more affordable, higher valued and more attractive.
Table of Contents
Steel Casting Design Videos
The SFSA Marketing Committee and staff have been working with Mike Gwyn with No Redesign to develop a series of steel casting design videos. The first four videos are now available to members on the Steel Wiki website. The video series, “Steel Casting Design & Manufacturing Engineering” is presented in the context of a story told by Mike of how he discovered innovative principles for excellence in steel casting design. The target audience for this series is OEM casting designers and buyers as well as steel casting producers.
The link to the wiki page is as follows: https://wiki.sfsa.org/index.php/SFSA_Steel_Casting_Design_%26_Manufacturing_Engineering. You will need to login to the wiki to view the page. Above each video is a shareable link to provide your customers for that video. With this link, a short form is required to access the video. A user will need to complete this form each time they watch a video. SFSA will receive an email for each form to track usage and to send a follow up email seeking feedback. A general email has been established for questions and feedback – design@sfsa.org.
76th T&O Conference
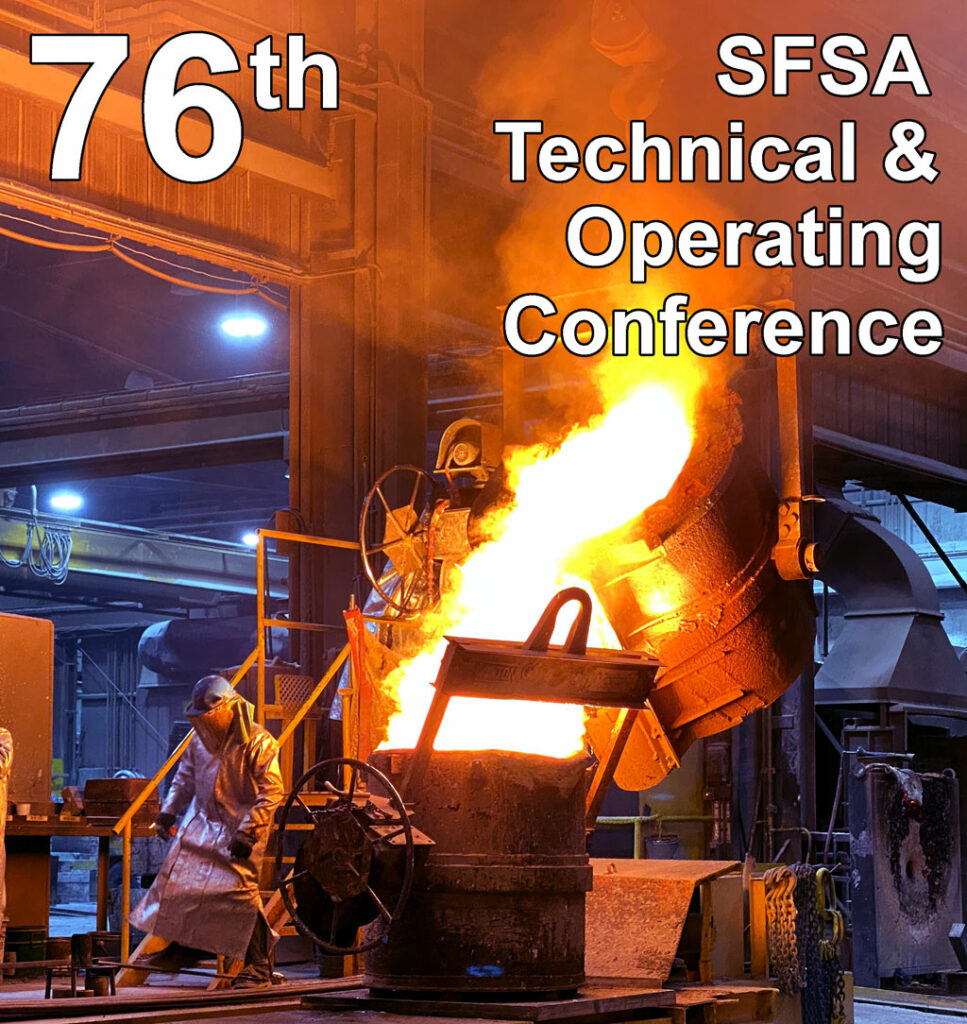
Supported by steel foundry members that make up the Society, the T&O conference is the premiere steel casting event in the world. The 76th conference will continue the legacy of technical and operating topics of today that will provide value to the industry for many years to come. This year’s workshop will highlight the future of manufacturing steel castings with automated welding, digital surface and fiber optic Industry 4.0 technology, advanced melting technology, and process control certification. The conference includes sessions related to Next Generation Manufacturing and casting simulation, and many more papers covering everything from melting to foundry engineering to molding to finishing to management to EHS to quality to technical & featured research.
Registration and hotel information are available here.
Please contact Dave with any questions.
SFSA EHS/HR Meeting
Please plan to attend the SFSA EHS & HR Group Meeting on October 26-27, 2022 at MetalTek – Wisconsin Centrifugal in Waukesha, WI. This meeting is a great opportunity to learn from your peers on many topics including how to improve EHS training and practices, communication, and the latest HR topics. In addition, a round-table discussion is the perfect forum to share practices and get answers to your EHS and human resource questions. There is no registration cost for the meeting – travel, hotel, meals, etc. are the attendees’ responsibility. Make your plans now to attend – https://sfsa.site-ym.com/events/EventDetails.aspx?id=1672378
Steel Casting Research
The July Casteel Reporter introduced SFSA’s research objectives. It also put forward an opportunity for industry to champion research projects by direct involvement in the steering and deployment; thus, obtaining an early and direct benefit from current R&D. In addition, an opportunity to propose new, non-competitive research ideas to SFSA’s research committees. To sponsor a project or submit a research project, please contact Dave. In this Reporter, we highlight our research thrust for Job Shop Industry 4.0 (I4). This thrust will advance manufacturing steel castings through Smart Automation (job shop steel foundry manufacturing), Smart Data (machine learning and IoT), and ARtisan (Augmented Reality work instructions, training, and video for AI/IoT). Unlike high production manufacturing, foundries are job shops that can not readily take advantage of part specific programming and fixturing used by traditional robots, nor Big Data. However, automation of foundry processes is crucial and can be achieved through research and development. Likewise, Small Data coupled with human intuition for analytics can guide process optimization and quality improvement. Wearable technology is common place for personal use, and will be pursued to enable the foundry artisan of the future. The development of I4 technology is critical to augment the workforce and advance manufacturing steel castings. The following projects support this thrust:
- Automatic Segmentation of Steel Radiograph Indications and Surface Fracture Porosity – University of Alabama at Birmingham
- Robotic Part Recognition and Grasp Detection – Deierling Engineering Consultants
- Arc Air Automation – Iowa State University
- Robotic Welding – Iowa State University
- Automated Grinding – Iowa State University
- Fiber Optics for Mold Gap Measurement – Missouri University of Science & Technology
- Identifying the Limiting Factors of Mechanical Properties by Autonomous and Quantitative Fracture Surface Analysis – Texas A&M University
SFSA utilizes a R&D project dashboard to provide an overview and status on activities. To learn more about the above projects, the dashboards are available here. For any additional information, please contact Dave.
Research Highlight – Chemistry Analysis Round Robin
Steel Founders’ Society is still conducting a chemistry analysis round robin to generate data on the reproducibility and repeatability of SFSA member foundries’ routine spectrographic analysis. If you participate you will be able to obtain the results and see where you stand compared to everyone else in industry and you will be helping society with improving industry standards. With this study of reproducibility and repeatability we will assess our measurement ability and compare it to the past, to see if we have improved in our capabilities. We will also see if an accurate reading of a material’s chemistry can better predict a material’s properties thus predicting better performance, to show if we can tailor our process to match chemistry.
If you would like to participate or have any questions please feel free to contact Ruth Berrios at ruth@sfsa.org.
Cast in Steel 2023
The competition will be held on April 24, in Cleveland, Ohio, and awards will be presented on April 25th in conjunction with the Presenting Sponsor AFS’ Metal Casting Congress which runs from April 25 – April 27. This year, teams have to design and cast an African spear point, weighing no more than 1kg and no more than 0.5m in length.
Our students can’t do this without having a great foundry partner. If your foundry is interest in partnering with a team, contact Raymond at monroe@sfsa.org or Renee at rmueller@sfsa.org.
For more detailed information about the competition visit Cast in Steel.
Market News
The August SFSA trends shows some softening in bookings as we near the fourth quarter. The 3/12 for steel casting bookings dipped below 10% year over year for the first time since March 2021. Similarly, stainless bookings dipped into negative year over year territory for the first time since December 2020. Shipments and backlogs remain stable and well above year ago levels as foundries continue to be challenged with labor shortages.
Looking ahead at the next quarter, only 21% of members anticipate an increase in business bookings with more than 70% expecting bookings to remain flat.
To see what may lie ahead for next year, the SFSA 2023 Market Forecast, presented last month at the SFSA Fall Leadership Meeting, is now available online here.
Casteel Commentary
Traditional manufacturing concentrated on either welding together standard mill shapes or machining features from a block of steel. Many, if not most steel products used are made by a combination of machining, welding fabrication and mechanical assembly to get the equipment performance needed. Steel casting for the early industrial age were the premium product, the only way to get complex part geometry and internal features in a steel part. Prior to the development of arc welding, mill products were riveted together. Electric arc welding allowed more sophisticated designs and geometries. Parts were designed on graph paper with calculations simplified and done on a slide ruler. New designs were qualified by full component testing to endure a reasonable service life and avoid premature failure.
Incremental, evolutionary design guided by new design concepts based on experience and field failures that led to higher performance in more complex parts with quality tests and inspections to ensure safety and reliability. ASTM, AWS D1.1, ASME BPVC, etc. developed material, design, inspection standards and codes that allowed rapid new equipment designs that proved to be safe, efficient and reliable.
Kids like to play by building things. A long time ago, when I was a kid, we had erector sets that let you build new things. These sets were similar to the way things were designed and built, assembling bars, beams, pipes and plates with bolts or rivets. Designs were formalized in 2D orthogonal drawings. The drawings were easy to make when the part was made from uniform sections of square components assembled in square shapes. Casting design was challenging because design engineers were trained to assemble mill products and fabrication gave sharp corners and uniform sections. They were designing with erector sets.
This changed with the advent of computational modeling. The big first commercial shift was the ability of designers to use solid models and test them for service with Finite Element Analysis (FEA). Now they no longer had to pretend the part was mainly a beam and approximate the loads and part response, they could model it. This coincided with the commercial pressure to accelerate the design process and eliminate the need to full component test each new design before accepting it. The move to solid models away from 2D drawings is an essential benefit for us as casting producers. With this innovation, our more complex casting geometries could demonstrate superior performance based on non-orthogonal designs.
But we still had a significant commercial barrier. The need to produce a tool prior to making the casting made it take longer and cost more during the developmental stage than fabrication and machining. Many ideal casting applications were made as poor fabrications or expensive machined components because the cost and time to produce pattern tooling during the design and test program made considering castings untenable.
We as casting producers were the early and first adopters of 3D printing for commercial production. 3D printed patterns for mold making or investment casting production were readily adopted for casting prototype production. Sand printing was developed and continues to expand, making castings more easily designed and tested without the expense or time of pattern tooling production.
3D printing of steel parts has been more recently seen as a production path to get complex geometries and materials not available even as a casting. The original 3D metal printing was for small components and was made from powder, layer by layer, slowly and expensively. The terminology shifted as larger components and other approaches replaced printing as the driver to create the shape. Using a robot with some form of welding became an alternative way to create these 3D shapes. The original powder bed technique that relied on fusing the powder at each level became Powder Bed Fusion (PBF). The use of robotics or gantry systems became Direct Energy Deposit (DED). Since these are not exclusively 3D printing, the current term of art is Additive Manufacturing (AM) to contrast with machining or subtractive manufacturing.
AM DED faces significant challenges to make large scale components that could replace castings. At the request of the Department of Defense, I have evaluated the potential to replace large scale critical castings with AM DED. The barriers are significant. AM DED has to address the limitations and challenges we know of welding large thick sections. Qualifying complex parts requiring high strength, toughness, etc is a major technical and performance hurtle for adopting AM DED. AM DED has to face the process control and other challenges of automated welding and then qualify the final component to the rigorous testing and inspection required for castings. There will be good and useful applications of AM DED, but they are likely to be limited.
But for us as casting producers, the interest and development of AM DED is likely to make steel castings a more attractive and easier to qualify as components for critical applications. Design engineers that like the geometric freedom of AM DED will see the same type benefits in steel casting capability. The use of printed or AM molds and tools will make the tooling cost and time become less of a factor. In fact, the ability to make tool-less castings will allow multiple design variants to be tested in parallel and result in more radical and higher performance castings. The testing and quality needs for AM DED mirror our needs. Solutions or approaches accepted for AM DED should translate over to our products.
I am optimistic that the incoming engineers for places like SpaceX will push the envelop for design and materials. Castings gives them affordable geometric freedom and unique opportunities to get high performance. We must take the initiative to find these daring customers and support their radical efforts to create the next generations of steel castings. We can become the premium product of steel for the future.
Raymond
STEEL FOUNDERS' SOCIETY OF AMERICA | ||||||||||
---|---|---|---|---|---|---|---|---|---|---|
BUSINESS REPORT | ||||||||||
SFSA Trend Cards (%-12 mos. Ago) | 12 Mo Avg | 3 Mo Avg | August | July | June | |||||
Carbon & Low Alloy | ||||||||||
Shipments | 10.7 | 7.2 | 8.5 | 1 | 12 | |||||
Bookings | 18.6 | 8.1 | 3 | 9.5 | 11.8 | |||||
Backlog (wks) | 13.7 | 13.1 | 12.3 | 13.1 | 14 | |||||
High Alloy | ||||||||||
Shipments | 10.8 | 15 | 3 | 22 | 20 | |||||
Bookings | 6.2 | -0.7 | -4 | 0 | 2 | |||||
Backlog (wks) | 12.8 | 12.4 | 12 | 12.7 | 12.4 | |||||
Department of Commerce Census Data | ||||||||||
Iron & Steel Foundries (million $) | ||||||||||
Shipments | 1,447.10 | 1,469.70 | 1,473 | 1,447 | 1,489 | |||||
New Orders | 1,523.70 | 1,444.00 | 1,463 | 1,450 | 1,419 | |||||
Inventories | 2,583.80 | 2,698.00 | 2,711 | 2,697 | 2,686 | |||||
Nondefense Capital Goods (billion $) | ||||||||||
Shipments | 80.5 | 80.8 | 82.1 | 80.7 | 79.8 | |||||
New Orders | 86.6 | 85.6 | 84.8 | 87.1 | 84.9 | |||||
Inventories | 208.8 | 212.8 | 213.6 | 212.9 | 212 | |||||
Nondefense Capital Goods less Aircraft (billion $) | ||||||||||
Shipments | 74.6 | 73.9 | 74.2 | 73.9 | 73.5 | |||||
New Orders | 76 | 74.9 | 75.7 | 74.7 | 74.2 | |||||
Inventories | 143.2 | 147.6 | 148.5 | 147.5 | 146.6 | |||||
Inventory/Orders | 1.9 | 2 | 1.96 | 1.97 | 1.98 | |||||
Inventory/Shipments | 0 | 2 | 2 | 1.99 | 2 | |||||
Orders/Shipments | 0 | 1 | 1.02 | 1.01 | 1.01 | |||||
American Iron and Steel Institute | ||||||||||
Raw Steel Shipments (million net tons) | 7.8 | 7.7 | 7.7 | 7.7 | 7.6 |