It is exciting when a problem that has long limited our industry has a potential solution that could dramatically improve our industry. Traditionally, designers have been concerned with the reliability and safety of steel castings, not due to the properties but due to concerns about the defects that may cause sudden and unexpected failures below the loads expected in service. Last month, we visited with young engineers in Munich that have proposed a design methodology that will allow us to provide assured performance using current NDT methods and casting quality standards. This month’s commentary outlines their approach and its possible benefit for us.
Table of Contents
76th T&O Conference
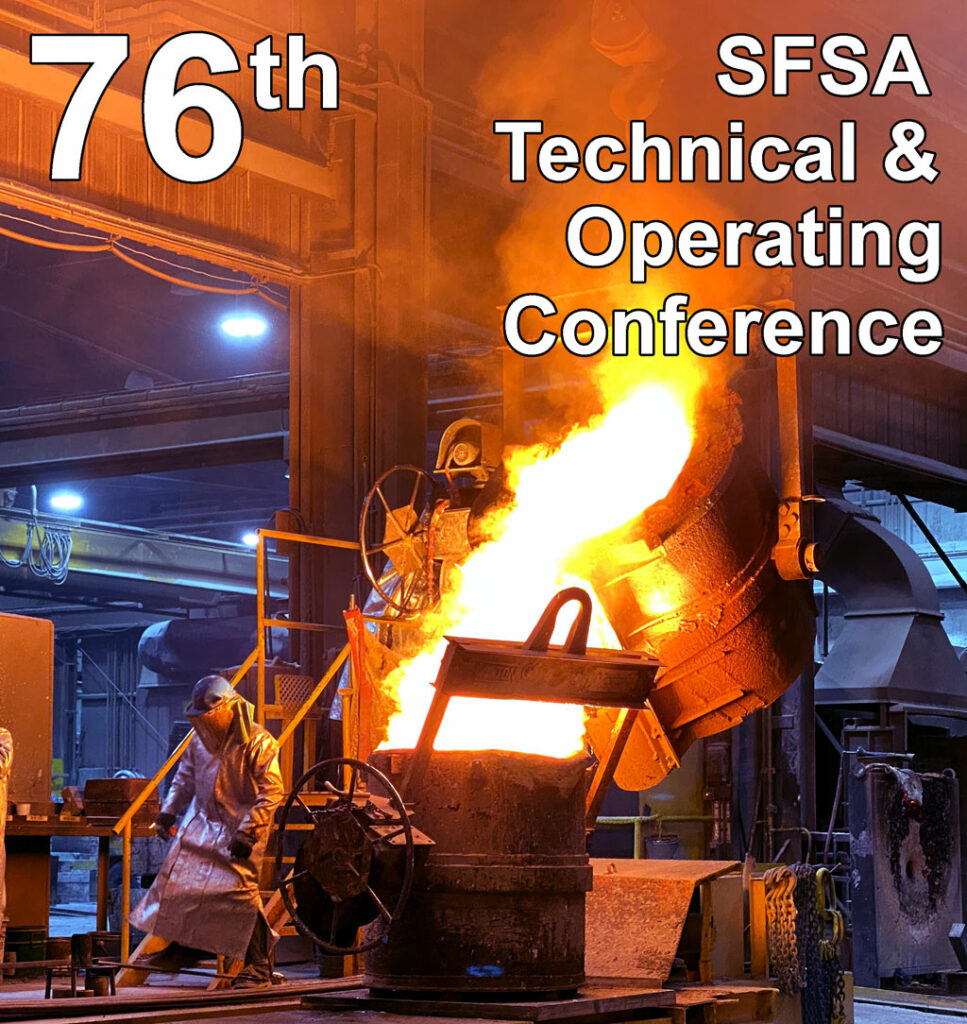
Final reminder to register for the 76th T&O Conference on December 7-10 in Chicago (hotel information can be found on the registration site – room block closes November 22). The conference program includes sessions related to Next Generation Manufacturing and casting simulation, and many more papers covering everything from melting to foundry engineering to molding to finishing to management to EHS to quality to technical & featured research. The T&O workshop highlights the future of manufacturing steel castings with automated welding, digital surface and fiber optic Industry 4.0 technology, advanced melting technology, and process control certification.
Steel Casting Research
The July Casteel Reporter introduced SFSA’s research objectives. It also put forward an opportunity for industry to champion research projects by direct involvement in the steering and deployment; thus, obtaining an early and direct benefit from current R&D. In addition, an opportunity to propose new, non-competitive research ideas to SFSA’s research committees. To sponsor a project or submit a research project, please contact Dave. In this Reporter, we highlight our research thrust for Hybrid and Advanced Manufacturing. This thrust creates pathways to new products, improved properties, and better manufacturing efficiencies including cost-effective, engineered composite materials. Hybrid manufacturing combines traditional processes such as forging to enhance properties in critical locations of a casting to provide higher performance. Creating steel geometries to be cast into steel gives opportunities not currently available such as improved heavy section properties and dual material castings. Advanced manufacturing improves primary and secondary processes such as pressurized casting or directed spray quenching. The development of hybrid and advanced manufacturing technology will provide future capability to create unique geometry, superior properties or cost-effective solutions. The following projects support this thrust:
- Determination of the Thermophysical Properties of Hot Toppings for Steel Ingots – Virginia Tech
- Demonstration of Novel Simulation for Accurately and Quantitatively Predicting Porosity in Steel Ingots and Castings – University of Iowa
- Clean Steel – University of Iowa
- Evaluation of Pressurized Molds – University of Northern Iowa
- Evaluation of Mold Washes – University of Northern Iowa
- Monel Alloys – Lehigh University
- Shaped Preforms for Castings – University of Alabama
- Encapsulated Inserts – University of Alabama
SFSA utilizes a R&D project dashboard to provide an overview and status on activities. To learn more about the above projects, the dashboards are available here. For any additional information, please contact Dave.
Cast in Steel 2023
The 2023 SFSA Cast In Steel (CIS) competition is anticipated to be the largest event since its inception in 2019. Forged In Fire’s David Baker will make his debut as a judge along with Ben Abbott, also from the popular History Channel show. Another first for 2023 is Colonel Ryan Howell, Ph.D., Program Manager of Main Battle Tank Systems will be a judge.
Teams will create an African Spear Point exploiting the casting manufacturing process from design conception to performance. The performance competition and awards ceremony will be held during the AFS Metalcasting Congress in Cleveland, Ohio on April 24-25, 2023.
SFSA staff promoted the competition and past winners at the FEF Industry Conference in Chicago earlier this month. Several faculty and students plan to enter a team. The registration deadline is December 30, 2022. To date, 12 teams have enrolled from the following schools:
University of Alabama at Birmingham (UAB)
Kent State University
Penn State University
Instituto Tecnológico de Morelia
Cal Poly Pomona (2 teams)
Penn State University – Behrend
Instituto Tecnológico de Saltillo (3 teams)
Pittsburg State University
Multiple University Team (Michigan Tech, MS&T, Georgia Southern, UW-Platteville, North Dakota College of Engineering
If your foundry is interest in partnering with a team, contact Raymond at monroe@sfsa.org or Renee at rmueller@sfsa.org.
Market News
In September, steel casting bookings remain above year ago levels but have been trending downwards for six months. Stainless bookings dipped further at 13.5% below September 2021 bookings. Shipments for steel and stainless castings remain relatively stable as do the backlogs with carbon and low alloy steel castings at 13 weeks and stainless at 12 weeks. Department of Commerce data shows iron and steel casting shipments and orders have been near parity since the second quarter of 2022. AISI reports that September steel shipments were down 7% from the previous month and 3% year to date compared to 2021.
The SFSA Marketing Committee will be meeting next month prior to the SFSA T&O Conference to finalize the 2023 SFSA Market Forecast. The committee would appreciate receiving your input on the markets that you serve in support of the forecast. Please take a moment to complete the market forecast survey: https://www.surveymonkey.com/r/SFSA_4Cast22. Responses are kept confidential and will be aggregated with other member responses. Markets included in the forecast are as follows:
Markets
- Rail/Transit – frames, couplings, bolsters, track components, etc.
- Mining Equipment – axle housing, frame components, suspension, gear case, etc.
- Mining Consumables – G.E.T., liners, hammers, grate plates, cement and aggregate components
- Construction Equipment – axle components, sprocket, end caps, transmission housing, etc.
- Truck – Class 8 – suspension brackets, brake components, axle spindles, fifth wheels, etc.
- Pump – housing, impeller, covers, bowls, etc.
- Valve – strainer bodies, bonnets, butterfly valves, etc.
- Oil & Gas – port adapters, brackets, levers, slip linkages, etc.
- Military – ground vehicle and maritime components
- Industrial Furnace & Oven Mfg. – furnace, heat treat, steel mill components – rollers, links, baskets, etc.
- Industrial Machinery – Industrial equipment parts – pulp & paper, food, shotblast – plates, wheels, sprockets, flanges
Casteel Commentary
Design engineers design thinking that the parts they use have uniform properties in every direction and in every location. That is never true. Steel casting loaded beyond their capacity have complex shapes and fain in the heaviest loaded section with the failure starting at the largest weak point making the failure appear brittle and cause by a “defect”. Trying to educate design engineers and reduce weaknesses in castings that initiate failures has been a path for more than 50 years. Charles Brigg’s with Project 80 and with work with Wallace at Case Western tried to assure and formalize ways to design steel castings for high performance with confidence.
Modern modeling techniques which allow the analysis of casting geometries create more conservative designs but also reveal sections in the casting that are heavily loaded in service. Current NDT standards are workmanship and do not address the effect of indications on performance.
More challenging in some ways is the material’s engineering communities identifying all indications in the material, even at the atomic scale as “defects”. By this definition, all materials are defective, but all materials fail if loaded beyond their capacity including “defect” free parts. To attempt to clarify this terminology, SFSA has suggested the term quality details to indicate things that are larger than the microstructure like inclusions and porosity but smaller than the NDT detection limits and random in size and location. How do we manage and assess the impact of quality details on performance in a model-based engineering analysis?
SFSA has spent a lot of effort trying to understand the effect of quality details on performance. The results of some of the analysis can be seen in Figure 1. For common engineering steels, the effect is to reduce the measured ductility but have a marginal effect on strength. Fracture sensitive high strength steels are more sensitive to these quality details.
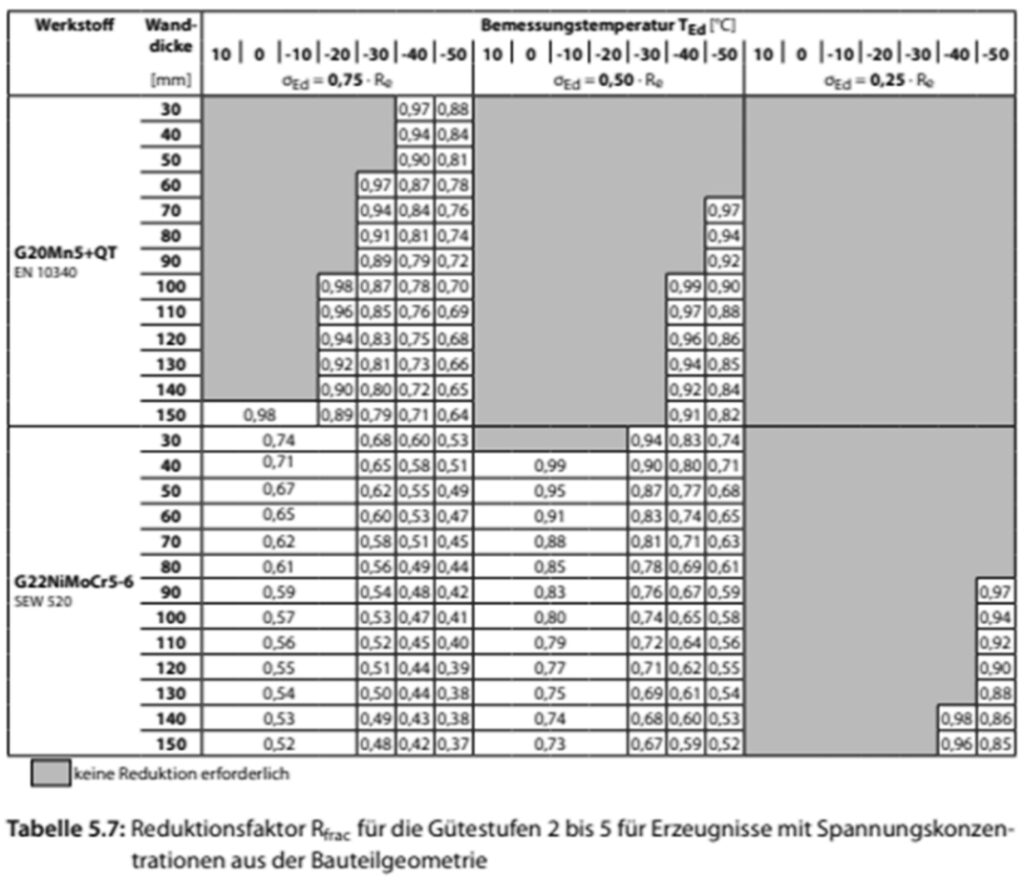
The new approach proposed by German investigators used fracture mechanics and placed the most damaging “defect” or quality detail in the most loaded section and calculated how large a quality detail could be tolerated safely. In other words, what size indication in NDT could be tolerated without compromising the safety or reliability of the structure. One benefit the investigators had was that they were Civil engineers and trying to find an engineering general solution instead of a detailed part by part approach.
For Figure 2, the reduction in allowable design strength based on quality details size, part thickness and service temperature are shown. This includes both a carbon and higher strength alloy steel. This graph is for the most detrimental quality detail on the most heavily loaded section. The level of quality required is highest at using 0.25 of the yield strength and highest when using 0.75.
This was extended into the main area of concern for design, fatigue. The analysis used the same approach, here defining then quality detail size by its area. The analysis was done with the most severe quality detail, a long sharp notch. The work was done both on surface and on internal details. The most severe standard that allows the highest design values was still less than the typical restriction in MT inspection of ¼ in. (6 mm). The quality detail requirements for levels are shown in Figure 3.
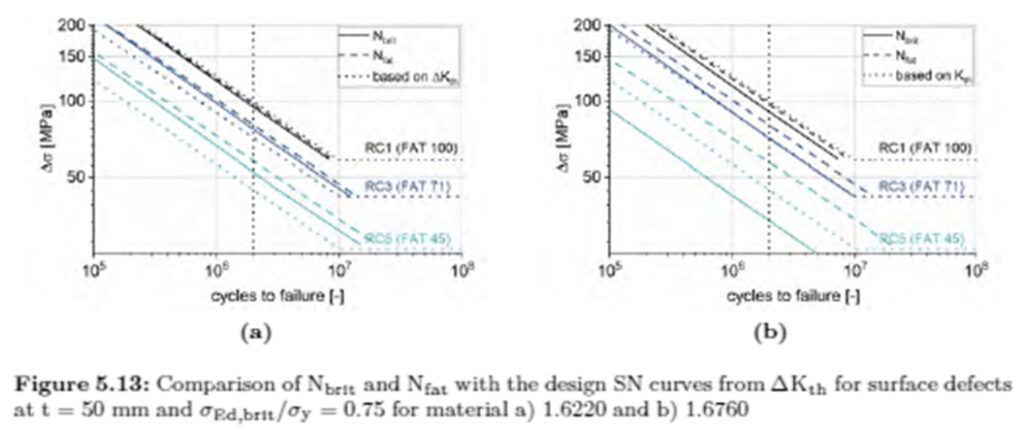
This approach gives results consistent with the industrial codes and practices like the ASME BPVC for both the NDT requirements and for the allowable stress for design. This looks like a huge step forward to allow us with our current program to validate the reliability of the approach and provide to the design engineering community a method of designing and specifying steel castings for structural applications with confidence.
Raymond
STEEL FOUNDERS' SOCIETY OF AMERICA BUSINESS REPORT | ||||||||||
---|---|---|---|---|---|---|---|---|---|---|
SFSA Trend Cards (%-12 mos. Ago) | 12 Mo Avg | 3 Mo Avg | September | August | July | |||||
Carbon & Low Alloy | ||||||||||
Shipments | 10.6 | 8.5 | 16 | 8.5 | 1 | |||||
Bookings | 18 | 6.3 | 6.5 | 3 | 9.5 | |||||
Backlog (wks) | 14 | 12.8 | 13 | 12.3 | 13.1 | |||||
High Alloy | ||||||||||
Shipments | 9.3 | 10 | 5 | 3 | 22 | |||||
Bookings | 3.3 | -5.8 | -13.5 | -4 | 0 | |||||
Backlog (wks) | 12.9 | 12.2 | 12 | 12 | 12.7 | |||||
Department of Commerce Census Data | ||||||||||
Iron & Steel Foundries (million $) | ||||||||||
Shipments | 1,460.00 | 1,475.30 | 1,495 | 1,484 | 1,447 | |||||
New Orders | 1,523.30 | 1,489.00 | 1,527 | 1,490 | 1,450 | |||||
Inventories | 2,607.00 | 2,697.30 | 2,693 | 2,702 | 2,697 | |||||
Nondefense Capital Goods (billion $) | ||||||||||
Shipments | 80.7 | 82.1 | 82.6 | 83.1 | 80.7 | |||||
New Orders | 87.1 | 87.6 | 89.4 | 86.2 | 87.1 | |||||
Inventories | 209.7 | 213.7 | 214.6 | 213.7 | 212.9 | |||||
Nondefense Capital Goods less Aircraft (billion $) | ||||||||||
Shipments | 74.4 | 73.9 | 73.8 | 74.1 | 73.9 | |||||
New Orders | 75.7 | 75 | 75 | 75.4 | 74.7 | |||||
Inventories | 144.3 | 148.7 | 149.9 | 148.6 | 147.5 | |||||
Inventory/Orders | 1.9 | 2 | 2 | 1.97 | 1.97 | |||||
Inventory/Shipments | 0 | 2 | 2.03 | 2.01 | 1.99 | |||||
Orders/Shipments | 0 | 1 | 1.02 | 1.02 | 1.01 | |||||
American Iron and Steel Institute | ||||||||||
Raw Steel Shipments (million net tons) | 7.7 | 7.5 | 7.1 | 7.7 | 7.7 | |||||